Influence Of Cutting Technology Of Digital Flatbed Cutter On Processing Quality
06/11/2019In order to minimize the cutting deformation of the digital flatbed cutter in the daily cutting and blanking of the metal steel plate, it is necessary to ensure the accurate and reliable positioning of the cloth before cutting. When conditions permit, the electromagnetic platform with multi-point contact is used for proper leveling treatment to eliminate the residual internal stress of uneven cloth and improve the flatness of the plate. The digital flatbed cutter is a kind of equipment which uses high speed, high temperature and high energy plasma cutting machine and computer control to cut cloth. Its working process is controlled automatically according to the pre-programmed program, and its identification is the processing program. Therefore, choosing a reasonable cutting process before processing - the starting point, direction, sequence, speed, etc. of cutting plays a decisive role in the processing quality of cutting pieces.
1. Selection of arc starting point
Generally, the arc starting point of the cutting piece should be at the edge of the cloth or in the middle of the cutting seam of the cut workpiece. When the distance is too large, the arc cannot be started or broken, which makes the cutting of the workpiece impervious, causing waste or scrap of the product; when the distance is too small, the nozzle is easy to be short-circuited between the nozzle and the workpiece, which will burn the nozzle and destroy the normal cutting process. It has been proved that the distance between the nozzle and the workpiece is generally 6-8mm, and the distance between the nozzle and the workpiece can be slightly less than 6-8mm.
2. Cutting direction selection
The correct cutting direction should ensure that the last cutting edge is separated from most of the motherboard. If it is separated from the motherboard too early, the surrounding corner frame is not enough to resist the thermal deformation stress in the cutting process, resulting in the displacement of the cutting part in the cutting process, and the size is out of tolerance.
3. Selection of cutting speed
Cutting speed is the relative moving speed between cutting torch and workpiece in the cutting process of the digital flatbed cutter. Appropriate cutting speed is an important condition for the cutting surface to be straight. The cutting speed depends on the thickness of the material plate, cutting current, gas type and flow, nozzle structure and proper drag. At the same power, increasing the cutting speed will cause the incision to become oblique. During cutting, the cutting torch shall be vertical to the workpiece surface, but in order to facilitate the removal of slag, it can be slightly tilted back (generally, the tilt angle is not more than 3). )Therefore, in order to improve productivity, the cutting speed should be as large as possible on the premise of ensuring the cutting penetration.
4. Influence of cutting sequence
Cutting sequence refers to the sequence of cutting several nested parts on the steel plate by digital cloth cutter. Generally, the principle of "first inside and then outside, first small and then large" shall be followed: first cut the inner contour (or nested parts in the inner contour), then the outer contour; first cut the parts with a small area, then the parts with large size. Otherwise, when cutting the inner contour or other small parts on the cloth, the deformation will occur, resulting in a scrap of the machined parts.
the digital flatbed cutter has the characteristics of multi-function, high efficiency, high speed, high precision, low labor intensity, and high automation. It is suitable for processing parts of many varieties, small batches, complex shapes, and frequent exchange. It is widely used in many industries such as automobile, locomotive, pressure vessel, chemical machinery, nuclear industry, general machinery, engineering machinery, steel structure, etc. Digital plasma cutting can cut all kinds of metal materials that are difficult to cut by oxygen (plasma arc can also cut some non-metallic materials). Its main advantages are that when cutting ordinary carbon steel sheet with small thickness, the cutting speed can reach 5-6 times of that of oxygen cutting method, the cutting surface is clean, the thermal deformation is small, the cutting width and the cutting surface angle are large, and special cutting torch is used when cutting sheet Or the process can obtain the cutting surface close to the vertical. The processing quality of the cutting parts of the digital flatbed cutter plays a key role in the whole product, so it is particularly important to effectively prevent the deformation of the processing parts.
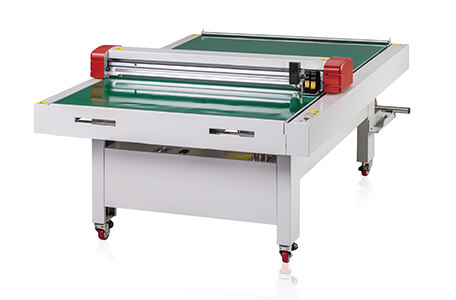
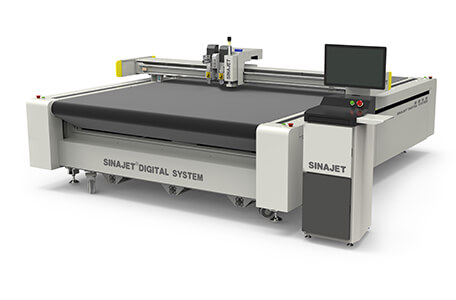



